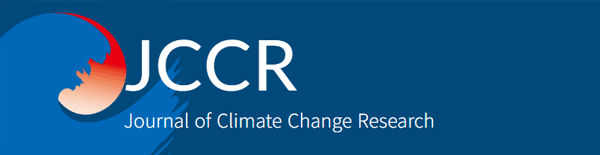
상업적으로 에틸렌카보네이트를 제조하기 위한 공정 조건 연구
Abstract
Among the exhaust gas, Carbon dioxide which is a causative factor in greenhouse effect. We study for synthesis of ethylene carbonate with carbon dioxide which is captured and utilized in commercially valuable. The Experiment was proceeded as pilot scale with using homogeneous organic catalyst which is able to produce ethylene carbonate in commercial and reaction conditions. Optimization condition for concentration of catalyst and reaction temperature, pressure was studied. We confirm that this process is eco‐friendly method and commercial application due to the mild condition and also catalyst has a competitive price, reusability.
Keywords:
Carbon dioxide, Ethylene oxide, Ethylene carbonate, Homogeneous organic catalyst1. 서 론
온실가스의 주범인 이산화탄소는 지구 온난화 현상의 원인이며 기후변화를 유발하고 있기에 이산화탄소를 사용하거나, 생성을 감축하기 위한 연구들이 계속 진행되고 있다.
이산화탄소는 무색, 무취, 무독성인 특성을 가지고 있으며 유기화합물로 변환될 수 있는 여러 가지 장점을 가지고 있다. (Lee et al. 2011; Geoffrey et al. 2004) 그리고, 이산화탄소는 가장 가격이 저렴하고 풍부한 탄소원료의 근원이기에 이산화탄소를 이용하여 실용 재료를 제조하는 연구도 이산화탄소를 감축시키기 위한 방법으로 활발히 진행 되고 있다. (Y. Hwang et al. 2006)
이산화탄소를 이용한 유기화합물 변환은 환경을 보호하고, 석유의존도가 높은 화학산업에서 자원의 가용성을 높일 수 있기에 충분히 가치 있는 활용 이라 할 수 있다. (Kember et al. 2011; Tahani et al. 2017) 이러한 연구가 활발히 진행이 되고 있기에 최근 보고서에 따르면 세계 시장에서 매년 2백만 톤의 이산화탄소가 사용된다고 한다. (Kim and Ryu et al. 2015)
이산화탄소는 우레아, 메탄올, 카보네이트류, 옥사졸리디논계 등 여러 유기화합물을 합성하는데 상업적으로 활용이 되고 있으며, 이 중 에틸렌카보네이트는 카보네이트 용매 중 가장 높은 분극화 능력을 제공하여 리튬염의 용해를 용이하게 한다. (Michael et al. 2016; Zhao et al. 2008; Hong et al. 2018; Bhanage et al. 2002) 또한, 전기화학적, 안정성, 낮은 점도와 어는점 등 다양한 특성을 가지고 있어 리튬이온 이차전지용 액체전해액으로서 사용된다. 그리고, 에틸렌카보네이 트는 디메틸카보네이트 합성에 있어서 맹독성과 부식성이 강한 포스겐의 대체물질로 사용이 가능하며, (Hong et al. 2002; Han et al. 2007) 디메틸카보네이트는 폴리카보네이트의 합성원료와 친환경 유기용매로도 사용이 가능하다.
본 연구에서는 Fig. 1과 같이 이산화탄소를 에틸렌옥사이 드와 고리부가반응 시켜서 에틸렌카보네이트를 합성하는 방법을 사용하여 에틸렌카보네이트를 상업적으로 생산하기 위한 설비를 구축하기 전 상업적으로 경쟁력이 있는 균일계 유기촉매 사용조건 및 공정조건을 확립하기 위한 실험 및 결과를 도출하고자 하였다.
2. 실험 및 방법
2.1 실험 물질
에틸렌카보네이트 합성을 위한 에틸렌옥사이드는 한화토탈에서 파이프라인으로 공급하는 99.9% 이상의 순도를 사용하였다. 파이브라인을 통해서 공급받는 에틸렌옥사이드는 별도의 저장탱크에 보관을 하고, 파일롯 실험 시 외부에 노출없이 바로 사용이 가능하다. 이산화탄소 (99.999%)는 molecular sieve 5A/12X (Aldrich)의 충진 컬럼을 통과시켜 수분을 제거하여 사용하였다. 실험에 사용된 촉매는 Table 1.과 같으며 충북대학교 촉매연구실에서 제조하여, 에틸렌카보네이트 합성이 충분히 검증된 아민계 유기촉매를 사용하였다. (M Hong et al. 2016)
2.2 합성 장비
에틸렌카보네이트 합성은 1 L 용량 SUS 304재질의 설계온도 200°C, 설계압력 100 bar의 교반이 가능한 고온, 고압반응기를 사용하였다. 전기를 이용한 가열용 맨틀을 사용하여 승온을 시키며, 반응기 내부 바이메탈 온도계가 연결되어있고, 냉각수를 반응기 내부 코일에 공급할 수 있어 온도 조절이 가능하다. 파이프라인을 통하여 파일롯 실험실로 공급되는 에틸렌옥사이드는 별도의 에틸렌옥사이드 저장용기 (SUS 304)에 받을 수 있어 소수점 첫째 자리 저울로 정량 확인이 가능하다.
합성된 에틸렌카보네이트의 순도 확인은 가스크로마토그래피 (동일시마즈, GC-2010, FID)를 이용하였으며 DB-WAX (30 m × 0.25 mm × 0.25 um) 컬럼을 사용하였다.
2.3 실험 방법
촉매를 반응기에 넣고 실험에 사용될 이산화탄소를 사용하여 반응기 기밀상태 확인 및 치환을 하였다. 에틸렌옥사이 드는 에틸렌옥사이드 저장용기에서 450 g (10.21 mol)을 정량하고 반응기에 사입 후 교반 및 승온을 시작하였다. 반응온도에 도달하였을 때, 이산화탄소를 반응기 압력과 동일하게 40 bar의 압력으로 주입하면서 반응을 진행하였다.
최적의 공정조건 확인을 위하여 에틸렌카보네이트 합성은 촉매종류, 촉매농도, 반응시간, 반응온도 별로 진행하고, 반응이 완료되면 60°C로 냉각 후 질소를 이용하여 미반응 에틸렌옥사이드를 제거 후 반응물의 질량을 확인하고, 가스크로마토그래피로 순도를 분석하였다.
에틸렌카보네이트 (분자량: 88.06 g/mol) 1 mol은 에틸렌옥사이드 (분자량: 44.05 g/mol)와 이산화탄소(분자량: 44.01 g/mol) 각 1 mol이 반응하여 합성된다. 위와 같이 진행된 실험에서 원료로 사용된 에틸렌옥사이드 450g (10.216 mol)에 동일한 몰 비율로 이산화탄소가 반응된 이론치 에틸렌카보네이트의 생성량 899.6g (10.216 mol) 대비 실험으로 회수된 반응물의 질량 비율로 전환율을 계산하고 비교해 보았다. 전환율 계산에서 실험으로 회수된 반응물의 질량은 가스크로마토그래피로 확인된 에틸렌카보네이트의 순도로 보정한 값을 사용하였다.
합성에 사용한 실험 장비는 Fig. 2와 같다.
3. 결과 및 고찰
상업적 생산에 적용 가능한 에틸렌카보네이트 공정 조건을 연구하기 위하여 촉매종류, 촉매농도, 반응시간, 반응온도에 따라 합성실험을 진행하고 확인된 전환율을 이용하여 결과를 비교해 보았다.
실험결과 반응시간이 증가될수록 전환율은 높아졌으며, 반응 3시간 후 촉매종류, 촉매농도, 반응온도 조건에 따른 에틸렌카보네이트 합성결과는 Table 2와 같다.
가스크로마토그래피를 이용한 순도분석결과 모두 98.5% 이상임을 확인할 수 있었으며, 실험에 사용된 3가지 촉매 모두 반응시간과 마찬가지로 촉매농도가 증가됨에 따라 에틸렌카보네이트의 전환율이 높아짐을 확인할 수 있었다.
각 촉매 별 농도, 반응온도에 따른 성능을 확인하기 위하여 Table 3과 같이 반응 3시간 후 에틸렌카보네이트의 전환율을 비교해 보았다.
실험결과 Catalyst NO. 2 농도 0.2 mol%를 사용하여 150°C에서 에틸렌카보네이트를 합성할 경우 가장 높은 98%의 전환율이 확인되었으며, Catalyst NO. 2, NO. 3 촉매를 이용하여 반응온도 130°C 이상에서 촉매농도 0.1 mol% 이상 사용하였을 경우 90% 이상의 전환율이 확인되어 충분히 공정에 적용 가능할 수 있을 것이라 판단된다.
Catalyst NO. 3의 경우 80°C 저온에서는 가장 높은 전환율을 보였지만, 온도가 130°C이상일 경우 Catalyst NO. 2보다 낮아지는 것을 확인 할 수 있었다. 이는 촉매의 Phenol 기에 치환된 Ether 그룹의 열 안정성이 떨어져 고온에서 일부 분해가 진행되어 나타난 결과로 판단된다.
합성된 에틸렌카보네이트를 온도 150°C, 진공 (5 torr이하) 조건에서 증류시켜 에틸렌카보네이트와 촉매를 분리시킬 수 있었다. 회수한 촉매의 재 사용시 성능 확인을 위하여 회수시킨 촉매와 반응에 사용하지 않은 촉매를 9:1 비율로 혼합 사용해서 에틸렌카보네이트를 합성하고 전환율을 확인해 보았다. 회수시킨 촉매와 반응에 사용하지 않은 촉매 9:1 비율로 혼합하였을 때 농도를 0.2 mol%, 반응온도 150°C, 반응시간 3시간으로 총 2회 촉매 재사용 실험을 하였으며, 그 외 실험조건은 이전 실험과 동일하게 진행하였다.
이전 실험과 같이 가스크로마토그래피를 이용한 순도분석 결과 모두 98.5% 이상임을 확인 할 수 있었으며, 이론치 에틸렌카보네이트 생성량 대비 반응 후 가스크로마토그래피로 분석된 순도로 보정한 생성물의 질량 값의 비율로 전환율을 확인한 결과는 Table 4와 같다.
Catalyst NO. 1, NO. 2의 경우 합성 후 회수한 촉매를 2회 재사용하여 에틸렌카보네이트를 합성에 사용한 결과 촉매를 처음 사용하여 합성한 에틸렌카보네이트의 전환율 대비 90% 이상의 전환율을 보이며, 재 사용 전 촉매의 성능을 거의 유지하는 것을 확인 할 수 있었다. 하지만 Catalyst NO. 3을 재사용 실험 한 결과 촉매를 처음 사용하여 합성한 에틸렌카보네이트의 전환율 대비 1차 재사용의 경우 91%, 2차 재사용의 경우 77% 수준으로 크게 떨어짐을 확인할 수 있었다. Catalyst NO. 3의 경우 에틸렌카보네이트 합성 실험 시 저온에서는 Catalyst NO. 2와 비교하여 상대적으로 높은 전환율을 보였지만, 고온에서 전환율이 낮아지는 결과와 마찬가지로 고온에서 촉매의 열분해로 인한 성능이 떨어지는 결과와 동일한 이유라고 판단되며, 고온반응 공정에서 촉매를 재 사용 시 반응 효율이 떨어질 가능성이 있기에 사용에 적합하지 않을 것으로 판단된다.
4. 결론
본 연구에서는 실험실 스케일로 성능이 확인된 알킬렌카보네이트 합성용 아민계 유기촉매를 사용하여 파일롯 스케일로 촉매종류, 촉매농도, 반응시간, 반응온도에 따라 에틸렌카보네이트를 합성하고, 전환율을 확인하여 에틸렌카보네이트의 상업적 생산을 위한 공정조건을 확인하고자 하였다.
실험 결과 반응시간을 오래하고, 반응온도, 촉매농도가 높아짐에 따라 전환율이 높아 지는 것을 확인할 수 있었으며, Catalyst NO. 2의 경우 촉매농도 0.2 mol%, 반응온도 150°C에서 98%의 높은 전환율을 보이며, 촉매농도 0.1 ~ 0.2 mol%, 반응온도 130 ~ 150°C에서 94% 이상의 전환율로 에틸렌카보네이트 제조가 가능함을 확인할 수 있었다.
합성된 에틸렌카보네이는 증류공정을 통하여 촉매를 제거할 수 있었으며 회수된 촉매를 재사용하여 성능 확인한 결과 재사용 전 합성 시 전환율 대비 95%이상의 전환율이 확인되어 공정 적용에 적합한 촉매임을 확인할 수 있었다.
본 연구를 통하여 에틸렌카보네이트 제조에 적용 가능한 공정 조건을 확인할 수 있었으며, 상업적 생산을 위한 반응기, 증류기 등의 제조시설 설계 및 운전 조건을 구축하는데 참고할 만한 결과를 얻을 수 있었다.
References
- Lee SH, Jeon JY, Lee BY. (2011) Synthesis of Low Molecular-weight Poly (Propylene Carbonate)-Poly (Ethylene Glycol) Block Copolymers through CO_2/Propylene Oxide Copolymerization. Clean Technology, 17, 244-249.
-
Geoffrey W. Coates and David R. Moore. (2004) Discrete Metal-Based Catalysts for the Copolymerization of CO2 and Epoxides: Discovery, Reactivity, Optimization, and Mechanism. Chem. Int. Ed, 43, 6618-6639.
[https://doi.org/10.1002/anie.200460442]
-
Hwang Y, Ree M, and Kim H. (2006). Catal. Today, 115, 288
[https://doi.org/10.1016/j.cattod.2006.02.061]
-
Kember M.R, Buchard A. (2011) Catalysts for CO2/epoxide copolymerization. Chem Commun, 47, 141-163.
[https://doi.org/10.1039/C0CC02207A]
-
Tahani A.G, Nada A.J, Ahmed A. (2017) Synthesis of Propylene Carbonate from Epoxide and CO2 Catalyzed by Carbon Nanotubes Supported Fe1.5PMo12O40. Journal of chemistry, 2017.
[https://doi.org/10.1155/2017/5641604]
-
Kim DH, Ryu SW. (2015) Synthesis and physicochemical properties of branched solide polymer electrolytes containing ethylene carbonate group. Journal of the Korean Electrochemical Society 18, 150-155.
[https://doi.org/10.5229/JKES.2015.18.4.150]
-
Michael M, Benjamin S, Sophie S, Hubert G Hydrolysis of Ethylene Carbonate with Water and Hydroxide under Battery Operating Conditions. Journal of The Electrochemical Society 163, 1219-1225.
[https://doi.org/10.1149/2.0411607jes]
-
Zhao X, An H, Wang S, Li F, Wang Y. (2008) Synthesis of ethylene carbonate from urea and ethylene glycol over zinc/iron oxide catalyst 83, 750-755.
[https://doi.org/10.1002/jctb.1872]
-
Hong MK, Kim YS, Kim HJ, Cho, HJ, Baik MH, Kim YJ. (2018) Scorpionate Catalysts for Coupling CO2 and Epoxides to Cyclic Carbonates: A Rational Design Approach for Organocatalysts. J. Org.Chem. 83, 9370-9380.
[https://doi.org/10.1021/acs.joc.8b00722]
- Bhalchandra B, Shin-ichiro F, Yanfeng H, Yutaka, I, Masayuki S, Kazuo T, Masahiko A. (2002) Concurrent Synthesis of Dimethyl Carbonate and Ethylene Glycol via Transesterification of Ethylene Carbonate and Methanol Using Smectite Catalysts Containing Mg and/or Ni. 83, 137-141.
- Hong ST, Park HS, Lim JS, Yoo KP. (2008) Synthesis of Dimethyl Carbonate from Methanol and Supercritical Carbon Dioxide over K2CO3/ZrO2 Catalysts. Korean Chem. Eng. Res, 46, 550-554.
- Han GB, Park NK, Yoon SH, Lee TJ (2007) Effect of the Additives on Direct Dimethyl Carbonate Synthesis using Methanol and Carbon Dioxide over Ce0.8Zr0.2O2. Catalyst Korean Chem. Eng. Res, 45. 554-559.
-
Hong M, Kim Y, Kim H, Cho HJ, Baik MH, Kim Y. (2016). The Journal of Organic Chemistry 83, 9370-9380.
[https://doi.org/10.1021/acs.joc.8b00722]