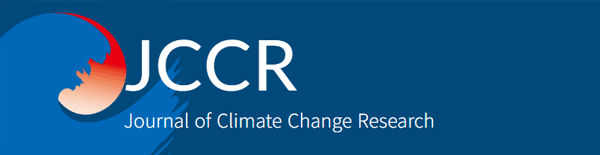
Electrocatalytic Reduction of Carbon Dioxide on Sn-Pb Alloy Electrodes
Abstract
Electrocatalytic reduction can produce useful chemicals and fuels such as carbon monoxide, methane, formate, aldehydes, and alcohols using carbon dioxide, the green house gas, as a reactant through the supply of electrical energy. In this study, tin-lead (Sn-Pb) alloy electrodes are fabricated by electrodeposition on a carbon paper with different alloy composition and used as cathode for electrocatalytic reduction of carbon dioxide into formate in an aqueous system. The prepared electrodes are measured by Faradaic efficiency and partial current density for formate production. Electrocatalytic reduction experiments are carried out at -1.8 V (vs. Ag/AgCl) using H-type cell under ambient temperature and pressure and the gas and liquid products are analyzed by gas chromatograph and liquid chromatograph, respectively. As results, the Sn-Pb electrodes show higher Faradaic efficiency and partial current density than the single metal electrode. The Sn-Pb alloy electrode which have Sn:Pb molar ratio=2:1, shows the highest Faradaic efficiency of 88.7%.
Keywords:
Carbon Dioxide, CCUS, Electrocatalytic Reduction, Formate1. INTRODUCTION
A certain level of electric potential should be applied between two separated electrodes to convert CO2 into valuable chemicals through electrochemical reduction of CO2 (Alvarez-Guerra et al., 2014). Electrochemical reduction of CO2 (ERC) provides a variety of attractive chemicals and fuels, such as methanol, formic acid, and other hydrocarbons (Ogura et al., 2010). CO2 is reduced on the cathode while the oxygen (O2) evolution reaction (OER) takes place on the anode. Half-reactions of the cathode for electrochemical CO2 reduction into major products such as carbon monoxide, formate, methane, and ethylene are listed below (Jhong et al., 2013). (pH 7 in aqueous solution vs. SHE(standard hydrogen electrode), room temperature, atmospheric pressure).
Among the number of products, conversion to formic acid/formate appears to have the best chance for the practical development of technically and economically viable processes (Oloman and Li, 2008). Accordingly, electrochemical reduction of CO2 to formic acid/formate gas had special attention in the literature over the last years.
It has been found that the electrocatalytic activities for the electro-oxidation of organic compounds are changed dramatically by the presence of sub-monolayer ad-atoms at optimum surface compositions, and that synergistic action between surface atoms is obtained (Watanabe and Motoo, 1975). Watanabe et al. (1991) have already investigated the catalytic properties of various copper-based alloy electrodes. In some cases the catalytic activity of the electrode is improved, such as Cu-Ni, Cu-Sn or Cu-Pb alloys, but in other cases the catalytic aptitudes of the metals are diluted, as it happens for Cu-Ag and Cu-Cd electrodes. Kyriacou and Anagnostopoulos (1992) used Au-modified Cu electrodes and observed that the production of CH4 falls when the surface contains more gold. The proportion of Au at the surface of the different electrodes did not exceed 7.2%. Christophe et al. (2012) used Cu-Au alloys with various Au contents (1∼50%) and reported that Au50Cu50 alloy appears to be the most efficient substrate for the conversion of CO2 into CO.
In this study, the Sn-Pb alloys were synthesized for electrochemical reduction of CO2 into formate in aqueous solution. The Sn-Pb alloy electrodes were obtained by electrochemical deposition with different compositions on a carbon paper. The oxidation and reduction behaviors of the electrodes were measured by cyclic voltammetry analysis. In addition, Faradaic efficiencies (FE) and partial current densities (PCD) for formate production on the alloy electrodes were obtained.
2. EXPERIMENTAL
2.1 Fabrication of Electrodes
Sn-Pb alloy electrodeposition is a typical binary co-deposition system. Pb2+ and Sn2+ can be reduced together at a lower overpotential, since their standard potentials are so close (-0.136 V for Sn and -0.126 V for Pb) without any additive agent [95]. Sn-Pb alloys as well as Sn and Pb electrodes were fabricated by electrodeposition on carbon paper as a substrate using convention al three electrode cell with a volume of 100 mL at 298 K under at mospheric pressure as shown in Fig. 1. The detailed procedure of the electrodeposition for the preparation of the alloy electrodes has been reported in our previous work (Choi, 2015; Choi et al., 2016). The molar ratios of Sn2+ to Pb2+ in the electrolyte for the electrodeposition of tin- lead alloys were 1:1, 2:1, and 8:1. The total concentration of metal cation in electrolyte was 10 mM for all experiments. The compositions of electrolytes to fabricate Sn, Pb, and Sn- Pb alloy electrodes used in this study are given in Table 1.
Electroreduction experiments were carried out at potentiostatic conditions with potentiostat/galvanostat using an H-type two compartment cell. It was designed to be separated into the two compartments of cathode and anode chambers by an ion exchange membrane (NafionⓇ 115) and to keep the gas pressure of the cathode chamber equal to atmospheric pressure during the electrolysis. An Ag/AgCl electrode saturated with KCl was selected as the reference electrode along with a Pt coil as the counter electrode. The cathode potential was controlled by -1.8 V against the Ag/AgCl reference electrode. An aqueous solution 0.5 M KHCO3 was used as catholyte, while 0.5 MKOH (Sigma Aldrich, 90%) was used as anolyte. A 0.5 MKHCO3 aqueous solution was saturated with CO2 by bubbling CO2 gas for 5 h before electrolysis. CO2 gas at a flow rate of 30 mL·min-1 was supplied continuously to the catholyte using glass sparger throughout the experiment, and the outlet gas stream was analyzed by gas chromatograph (GC; YL Instrument, 6500GC system), equipped with both thermal conductivity detector (TCD) and flame ionization detector (FID). Liquid samples were taken at 20 min intervals of operation time from the cathode chamber via a syringe septum, and analyzed using a high performance liquid chromatograph (HPLC; Themo Scientific, Ultimate 3000) to determine the amount of produced formate.
The electroreduction performance of the electrodes was measured by Faradaic efficiency and the partial current density of formate production. The Faradaic efficiency for formate production was calculated using the following equation:
(1) |
Where nfromate is the number of moles of formate produced, N is the number of electrons for formate produced, F is the Faradaic constant, and C is the total charge of electrons passed across the electrode duration of electrolysis. The partial current density (PCD) for formate production was calculated:
(2) |
3. RESULTS AND DISCUSSIONS
Potential screening test was performed using Sn, Pb, and Sn-Pb alloy electrodes with different reduction potentials at a potential range from -1.6 V to -2.2 V (vs. Ag/AgCl) at 0.2 V intervals to find out the optimum reduction potential. In all the cases, aqueous solutions of CO2-saturated 0.5 MKHCO3 and 0.5 MKOH were used in a H-type cell as a catholyte and a anolyte; respectively, during which CO2 gas (99.999% (v/v)) was continuously bubbled into the catholyte solution, and the cell temperature was maintained at 298 K. The catholyte was analyzed using HPLC after electrolysis to determine the amount of formate produced. The electro reduction performances such as Faradic efficiency and partialcurrent density of the electrodes can be calculated by equation (1) and (2), respectively. Fig. 2 shows the Faradaic efficiencies for the electrodes as a function of reduction potential. As shown in Fig. 2, the maximum Faradaic efficiency was obtained at -1.8 V (vs. Ag/AgCl) among the selected potential conditions for all the tested electrodes, and the Faradaic efficiency was decreased as the potential decreases further due to H2 evolution reaction. We can see during the experiments that bubbles form and increase fast on the surface of working electrode, which can be certainly attributed to the enhancement of H2 evolution at more negative potentials.
Electroreduction experiments were carried out under chronoamperometric conditions for 2 h at constant potentials of -1.8 V (vs. Ag/AgCl) in H-type cell. Fig. 3 shows the Faradaic efficiencies of the electrodes at -1.8 V (vs. Ag/AgCl). The Faradaic efficiency at 20 min was increased with tin content from 0% (Pb electrode) to 66.7% (Sn-Pb (21) electrode) and then started to decrease for electrodes with higher tin content than that of Sn-Pb (21) electrode (e.g. Sn-Pb (81) and Sn electrodes). The Sn-Pb (21) electrode showed the highest Faradaic efficiency of 88.7%, while the Pb electrode showed the lowest Faradaic efficiency (70.7%) among the tested electrodes. This result can be explained by the synergetic effect based on the high electric conductivity and the high electrocatalytic activity of Pb0 content of the alloy electrodes. The surfaces of Sn-Pb alloy electrodes have higher electrical conductivity compared to Sn and Pb, and the conductivity of the electrode surface increased as tin content increases in the alloys (Choi et al., 2016). In addition, they reported that the metallic lead (Pb0), which have higher conductivity and catalyticactivity than PbO, can be exist by tin content in the alloys, because tin inhibit the formation of less conductive PbO film at the surface. On the contrary, the Pb electrode showed the lowest Faradaic efficiency, because it has no Sn content and has the lowest electrical conductivity due to less-conductive PbO film at the surface. Except for the Pb electrode, there was some decrease in Faradaic efficiency about 4% with operation time from 20 to 120 min, and the partial current densities were maintained stably over the operation time. In the case of Pb electrode, both the Faradaic efficiency and the partial current density were decreased by c.a. 22% at the same condition.
Fig. 4 shows the partial current densities of the electrodes at -1.8 V (vs. Ag/AgCl). Generally, the partial current density was increased as the tin content increases, because the catalytic active area of the electrode increased with decreasing the PbO content at the surface. The Sn-Pb (21) showed the highest partial current density of 25.1 mA·cm-2 among the alloy electrodes. It is considered that the relative high partial current density of the Sn-Pb (21) electrode comes from the high Pb0 content, which has high catalytic activity for electroreduction of CO2 into formate.
Gas products from the electroreduction of CO2 were analyzed by GC at 20 min intervals during operation time of 120 min. From the GC analysis, it was confirmed that the main products in gas phase are H2 and CO. Fig. 5 shows the Faradaic efficiencies for H2 evolution for the tested electrodes at -1.8 V (vs. Ag/AgCl) over a period of 120 min. The Faradaic efficiencies were increased with operation time. In addition, Pb electrodes showed the highest Faradaic efficiencies for H2 evolution. The electroreduction of CO2 competes with H2 evolution reaction (HER) at the tested potentials, and the HER reduces the Faradaic current efficiency for formate production by consuming electrons. Therefore, the decrease of Faradaic efficiency for formate production is directly related to the increase of H2 evolution. When compare Fig. 5 with Fig. 3, the Faradaic efficiencies for H2 evolution and formate production show opposite tendency to the operation time and the composition of electrodes. Consequently, the increase of Faradaic efficiency for H2 evolution with operation time results in the decrease of Faradaic efficiency for formate production with operation time, and an electrode which showed high Faradaic efficiency for formate production has low Faradaic efficiency for H2 evolution.
Fig. 6 shows the Faradaic efficiencies of the tested electrodes for CO production at -1.8 V (vs. Ag/AgCl). The CO gas is also the conversion product from the electroreduction of CO2 like a formate. Thus, the time behavior of Faradaic efficiencies for CO production was similar to that for formate production. However, the Faradaic efficiencies for CO production showed different tendency to the composition of electrode compared to those for formate production. Generally, a higher Faradaic efficiency for CO production was obtained from an electrode which has higher tin content. This result coincides well with the literature (Hori, 2008), which reported the order of CO selectivity of metals: Au > Ag > Cu > Zn >> Cd > Sn > In > Pb > Tl ≈ Hg.
4. CONCLUSION
Sn-Pb alloy electrodes were prepared by electrochemical deposition with different compositions on a carbon paper to use as the cathode for the electroreduction of CO2 into formate. From the electroreduction experiment, the maximum Faradaic efficiency was obtained at -1.8 V (vs. Ag/AgCl). Generally, the Sn-Pb alloy electrodes showed high Faradaic efficiencies and high partial current densities compared to Sn and Pb electrodes. In addition, the Sn-Pb (21) electrode showed the highest Faradaic efficiency at -1.8 V (vs. Ag/AgCl). Consequently, the Sn-Pb alloy electrodes are more favorable to produce formate from electroreduction of CO2 than single metal electrodes (e.g. Sn and Pb electrodes) due to the high electrical conductivity, increased with tin content in the alloys, and the high electrocatalytic activity from the Pb0 content in the alloys. Consequently, the best performances in electrochemical CO2 reduction into formate such as Faradaic efficiency and PCD off or mate production were obtained on Sn-Pb (21) electrode at a reduction potential of -1.8 V (vs. Ag/AgCl).
Acknowledgments
This work was conducted under framework of the research and development program of the Korea Institute of Energy Research (B6-2519).
REFERENCES
-
Alvarez-Guerra, M, Castillo, AD, Irabien, A, (2014), Continuous electrochemical reduction of carbon dioxide into formate using a tin cathode: Comparison with lead cathode, Chem Eng Res Des, 92, p692-701.
[https://doi.org/10.1016/j.cherd.2013.11.002]
- Choi, SY, (2015), A study on the electrochemical reduction of carbon dioxide into formic acid using Sn-Pb alloy electrocatalysts, Dissertation, Chungnam National University.
-
Choi, SY, Jeong, SK, Kim, HJ, Baek, IH, Park, KT, (2016), Electrochemical reduction of carbon dioxide to formate on tin-lead alloys, ACS Sustainable Chem Eng, 4, p1311-1318.
[https://doi.org/10.1021/acssuschemeng.5b01336]
-
Christophe, J, Doneux, T, Buess-Herman, C, (2012), Electroreduction of carbon dioxide on copper-based electrodes: Activity of copper single crystals and copper-gold alloys, Electrocatal, 3, p139-146.
[https://doi.org/10.1007/s12678-012-0095-0]
- Hori, Y, (2008), Electrochemical CO2 reduction on metal electrodes, in modern aspects of electrochemistry, Springer, New York, p89.
-
Jhong, HR, Ma, S, Kenis, PJA, (2013), Electrochemical conversion of CO2 to useful chemicals: Current status, remaining challenges, and future opportunities, Current Opinionin Chemical Engineering, 2, p191-199.
[https://doi.org/10.1016/j.coche.2013.03.005]
-
Kyriacou, G, Anagnostopoulos, A, (1992), Electrochemical reduction of CO2 at Cu+ Au electrodes, J Electroanal Chem, 328, p233-243.
[https://doi.org/10.1016/0022-0728(92)80181-3]
-
Oloman, C, Li, H, (2008), Electrochemical processing of carbon dioxide, Chem Sus Chem, 1, p385-391.
[https://doi.org/10.1002/cssc.200800015]
-
Ogura, K, Ferrel, III JR, Cugini, AV, Smotkin, ES, Salazar-Villalpando, MD, (2010), CO2 attraction by specifically adsorbed anions and subsequent accelerated electrochemical reduction, Electrochim Acta, 56, p381-386.
[https://doi.org/10.1016/j.electacta.2010.08.065]
-
Watanabe, M, Motoo, S, (1975), Electrocatalysis by ad-atoms: Part III. enhancement of the oxidation of carbon monoxide on platinum by ruthenium ad-atoms, J Electroanal Chem, 60, p275-283.
[https://doi.org/10.1016/S0022-0728(75)80262-2]
-
Watanabe, M, Shibata, M, Katoh, A, Sakata, T, Azuma, M, (1991), Design of alloy electrocatalysts for CO2 reduction: Improved energy efficiency, selectivity, and reaction rate for the CO2 electro reduction on Cu alloy electrodes, J Electroanal Chem, 305(2), p319-328.
[https://doi.org/10.1016/0022-0728(91)85528-W]